Meet CRL’s big machines
Valerie and Gomer
Both machines played key parts in the early stages of the City Rail Link construction.
Pipe jacking is a trenchless construction method used to install pipelines beneath highways, railroads, harbours, rivers, and environmentally sensitive areas. Generally, pipe jacking involves a micro tunnel boring machine (MTBM) travelling from a launching shaft to a reception shaft.
CRL used the pipe jacking method to create a new stormwater main along the eastern side of Albert Street, between Swanson and Wellesley Streets with caisson shafts to be constructed at Wellesley and Swanson Street intersections. Two additional shafts were constructed in Victoria Street to enable strengthening of the Orakei Sewer Main across Albert Street.
Victoria Street shaft
Traditiional pile driving rigs are usually composed of a tall framework in which either a weight is raised and dropped on a pile head or in which a steam hammer drives the pile.
However CRL utilised a Cased Continuous Flight Auger piling rig which does not require a weight to be dropped. This technique is quieter and has less vibration compared to traditional piling. Also the cased nature provides improved ground support during piling.
Valerie
'Valerie’, was the 2m-wide tunnel-boring machine simultaneously excavating and installing a new stormwater pipe under Albert Street.
The tunnel boring machine (TBM) also known as a "mole" excavates tunnels with a circular cross section through a variety of soil and rock strata. TBMs are able to bore through anything from hard rock to sand.
Tunnel diameters can range from a metre (micro-TBMs) to around 19m.
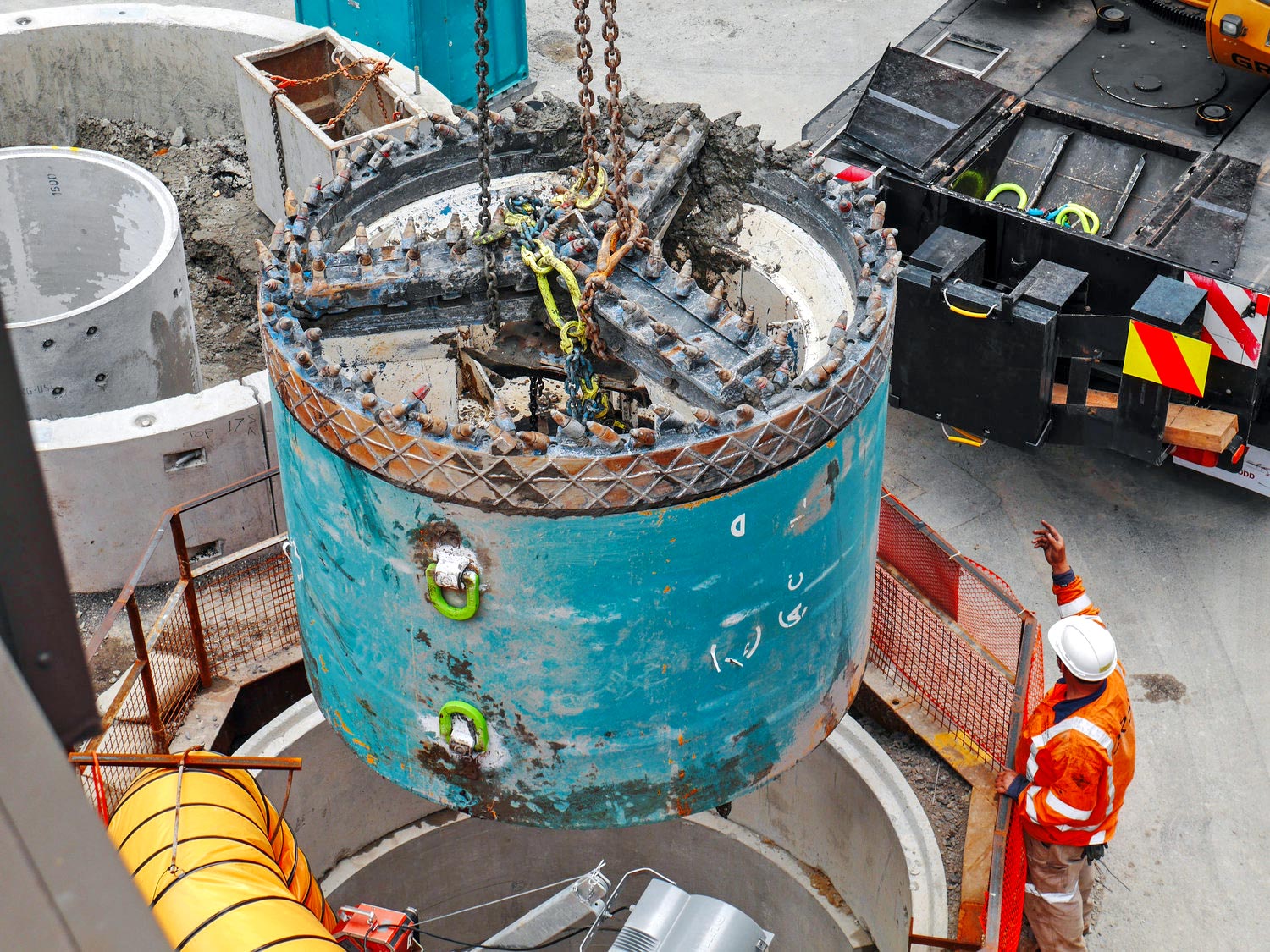
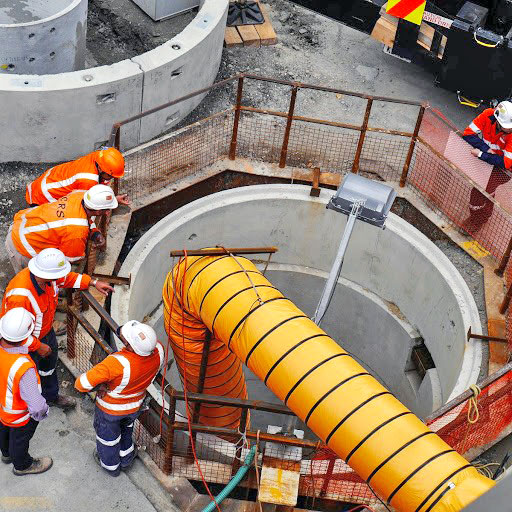
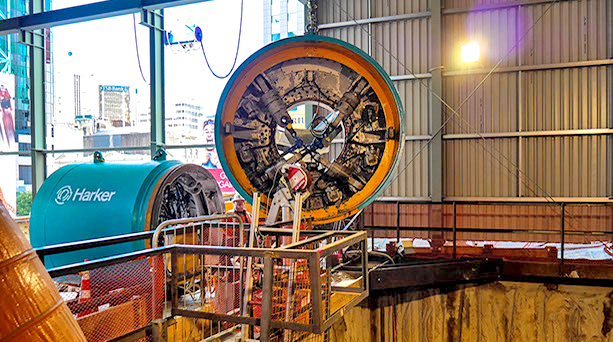
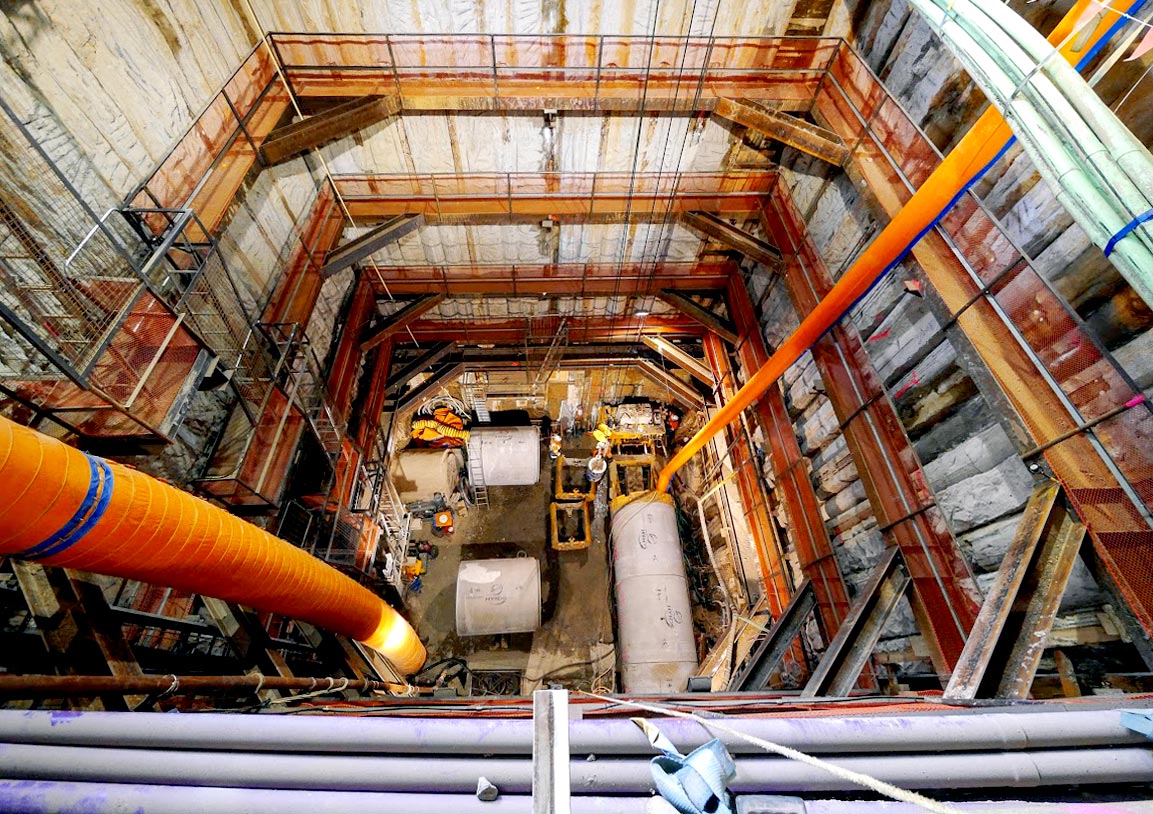
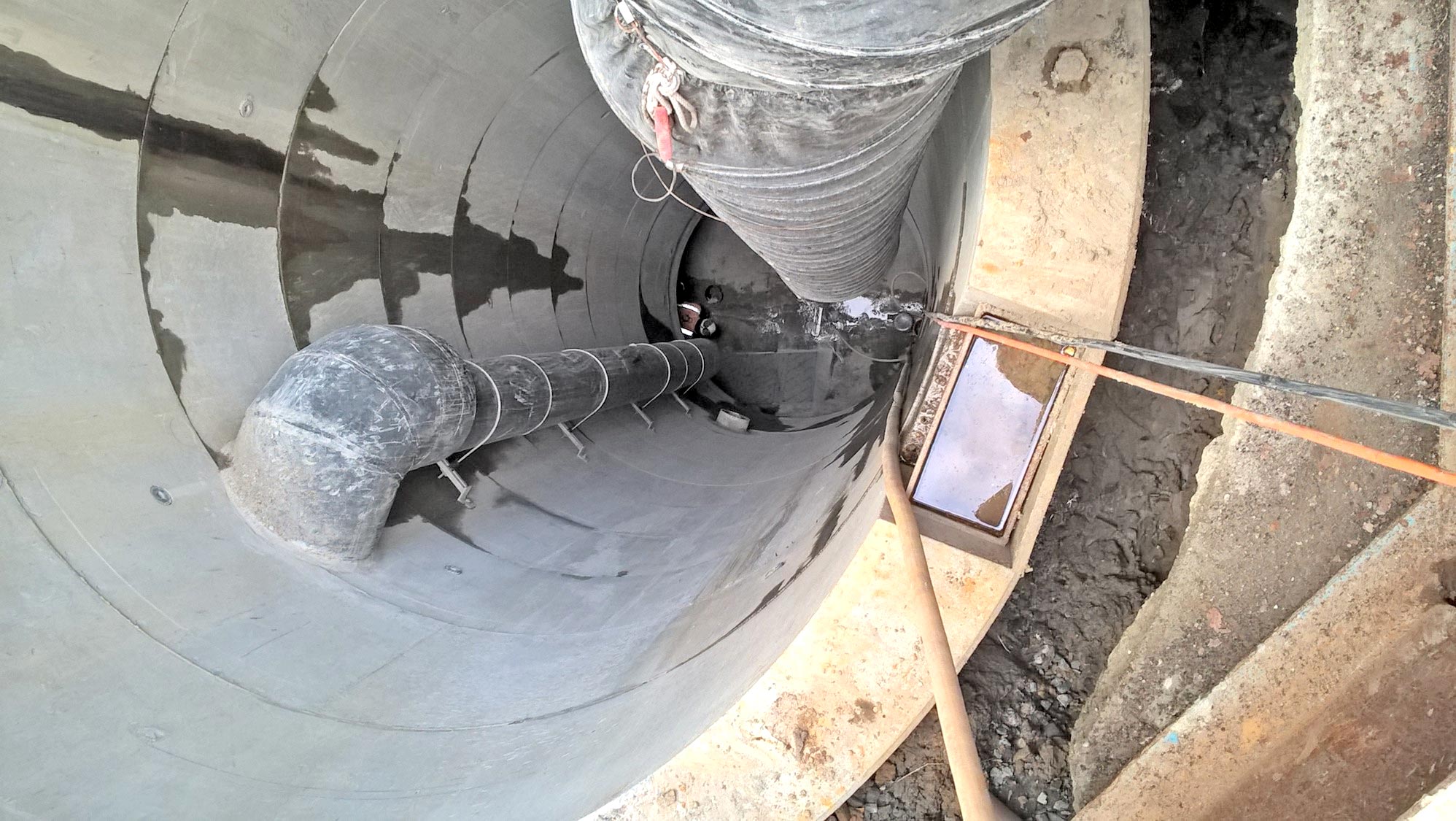
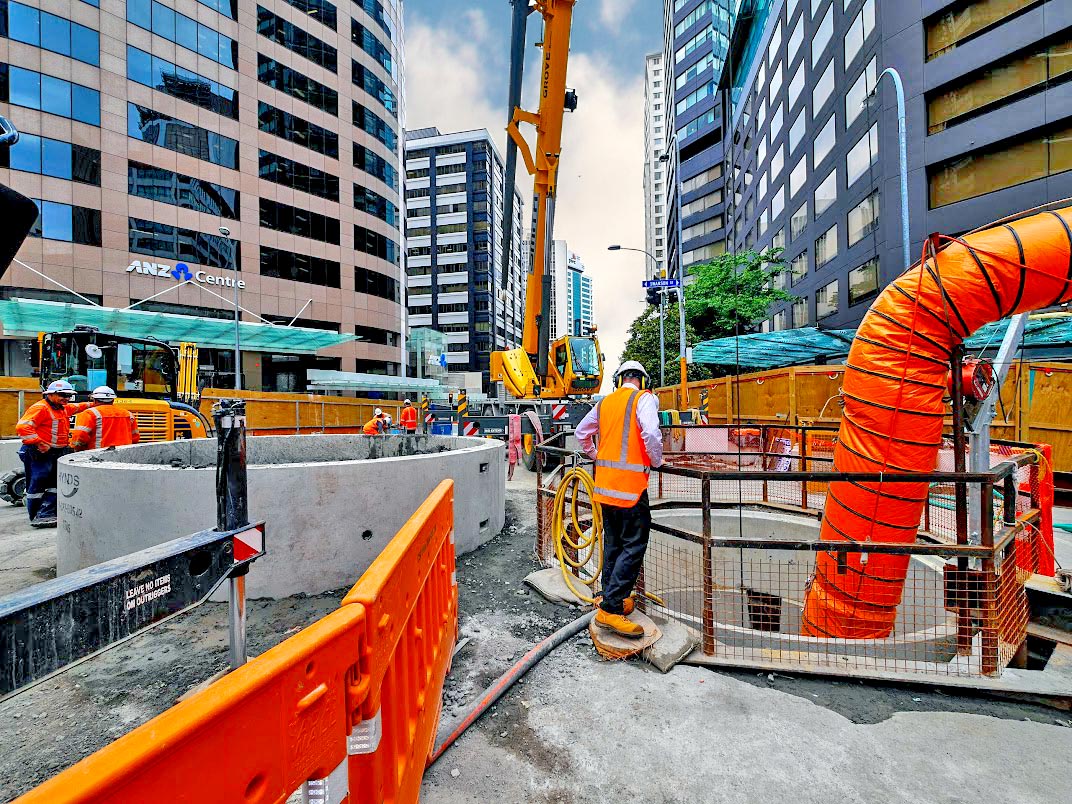
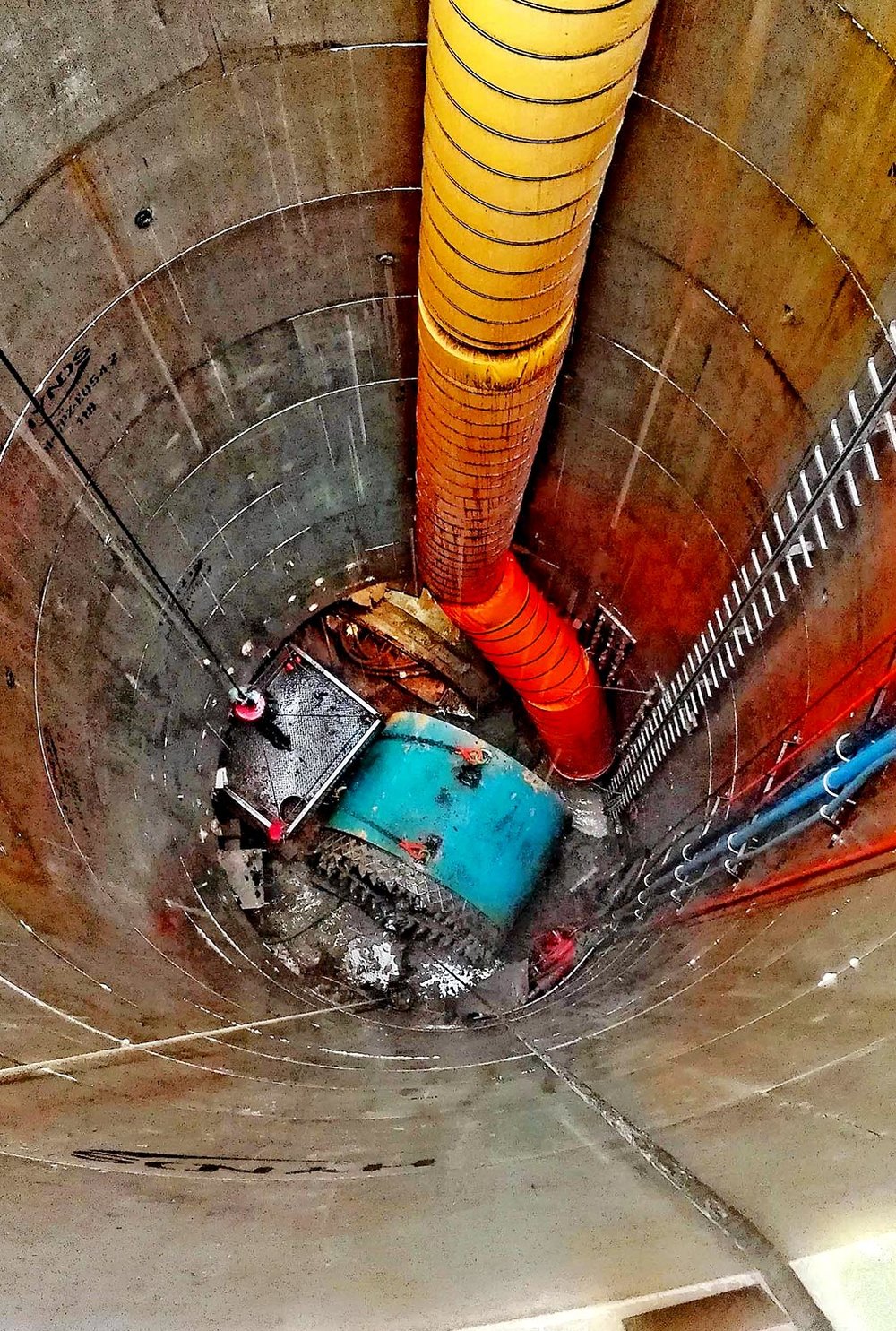
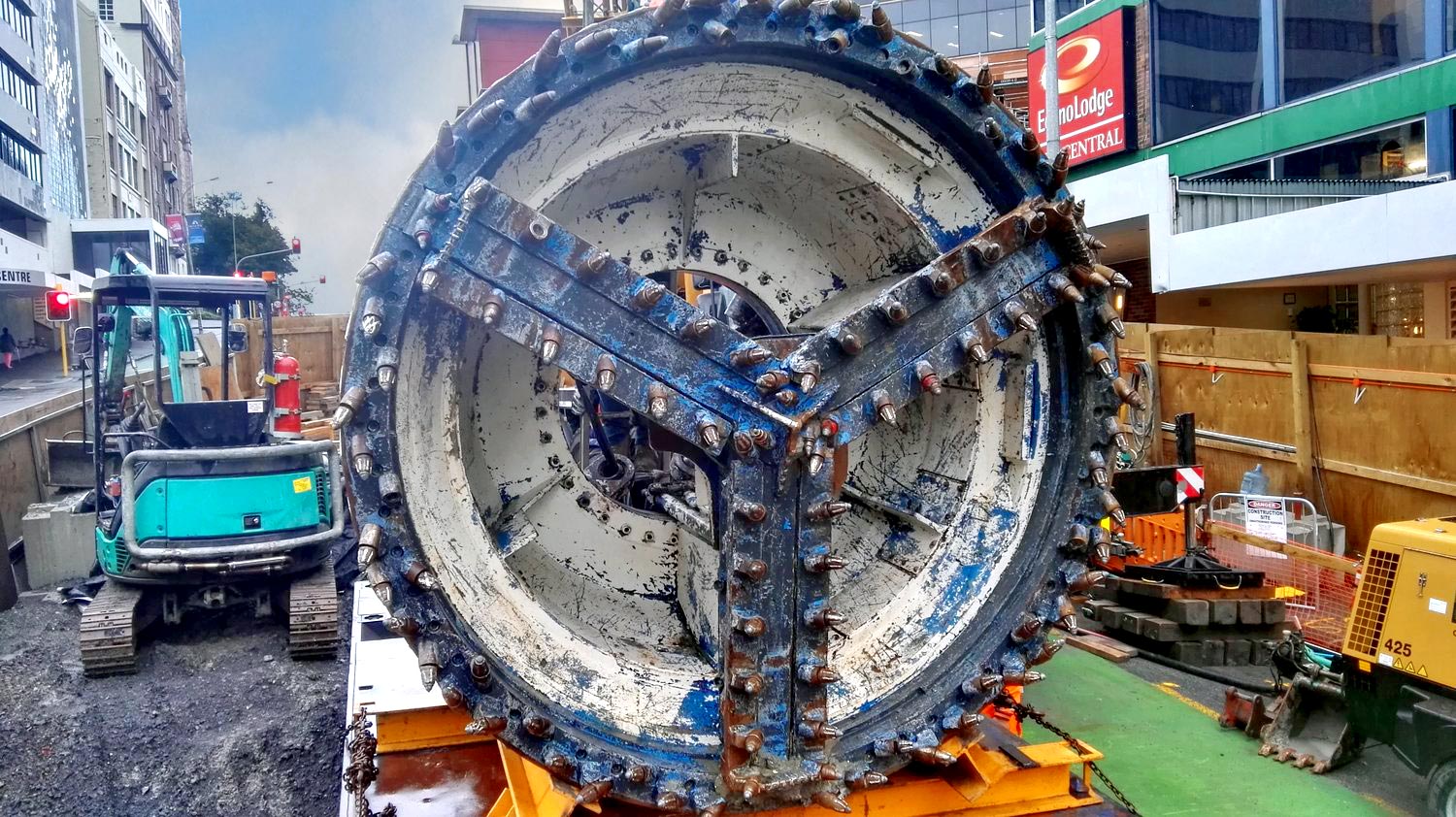
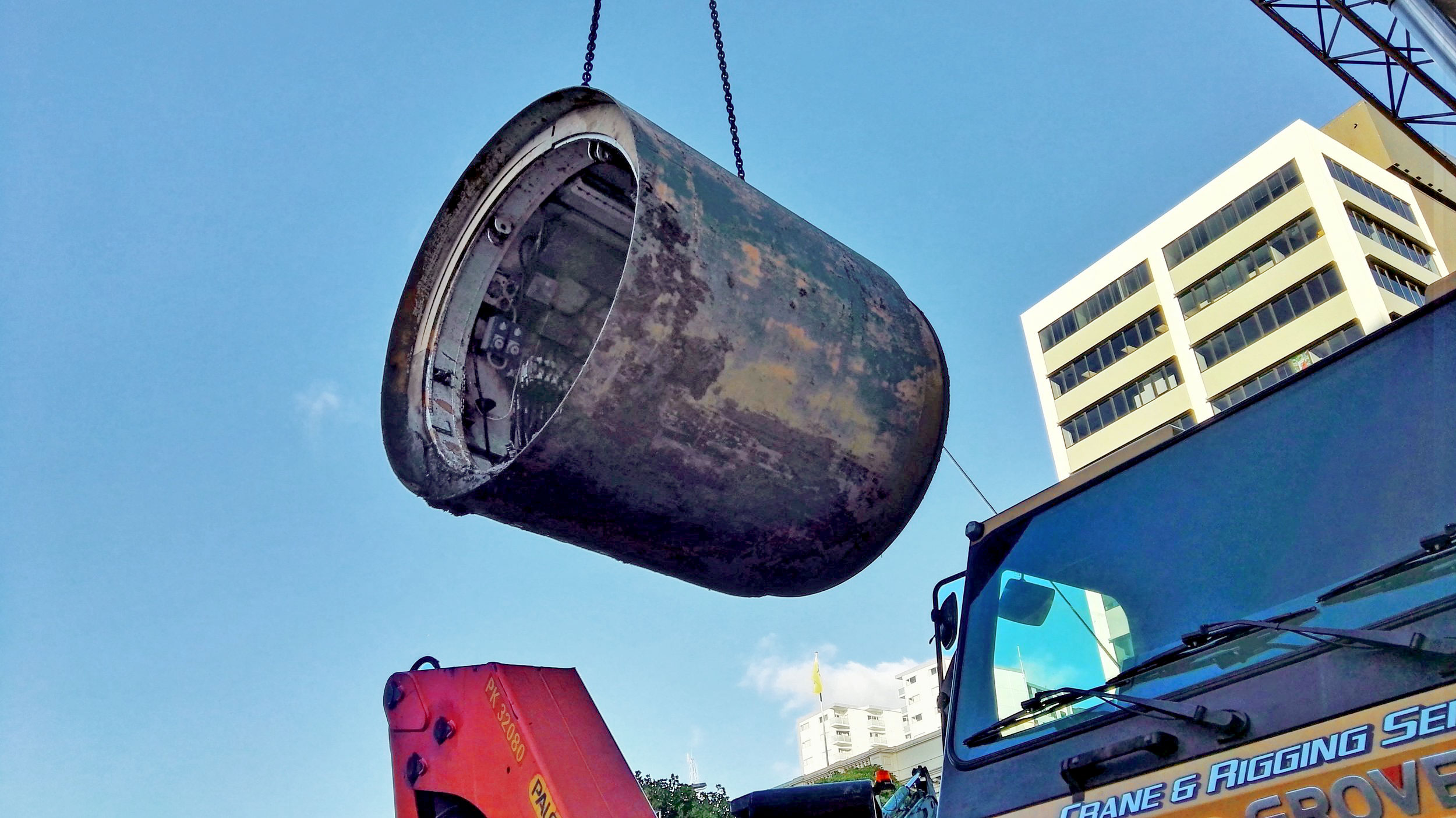
And the name?
Valerie was named as such by school children in a contest in praise of the mighty Olympic shot-putter Dame Valerie Adams. It started tunnelling and pipe-jacking work from the Victoria Street on 21 November 2015. By the time she arrived at the Swanson Street reception shaft early 2017, she had travelled 290m.
Valerie was returned to the launching shaft and travelled another 200m in the opposite direction - 490m in total.
In late April 2017, Valerie was pulled out of the Victoria Street shaft after finishing the stormwater work.
Gomer
‘Gomer’ was a nine-storey-high piling rig used on Albert St.
In all, Gomer dug 372 piles of up to 20m deep.
And the name?
It was affectionately named after 1960s TV character Gomer Pyle. Howard McNear played a car mechanic in the long-running American sit-com The Andy Griffith Show.
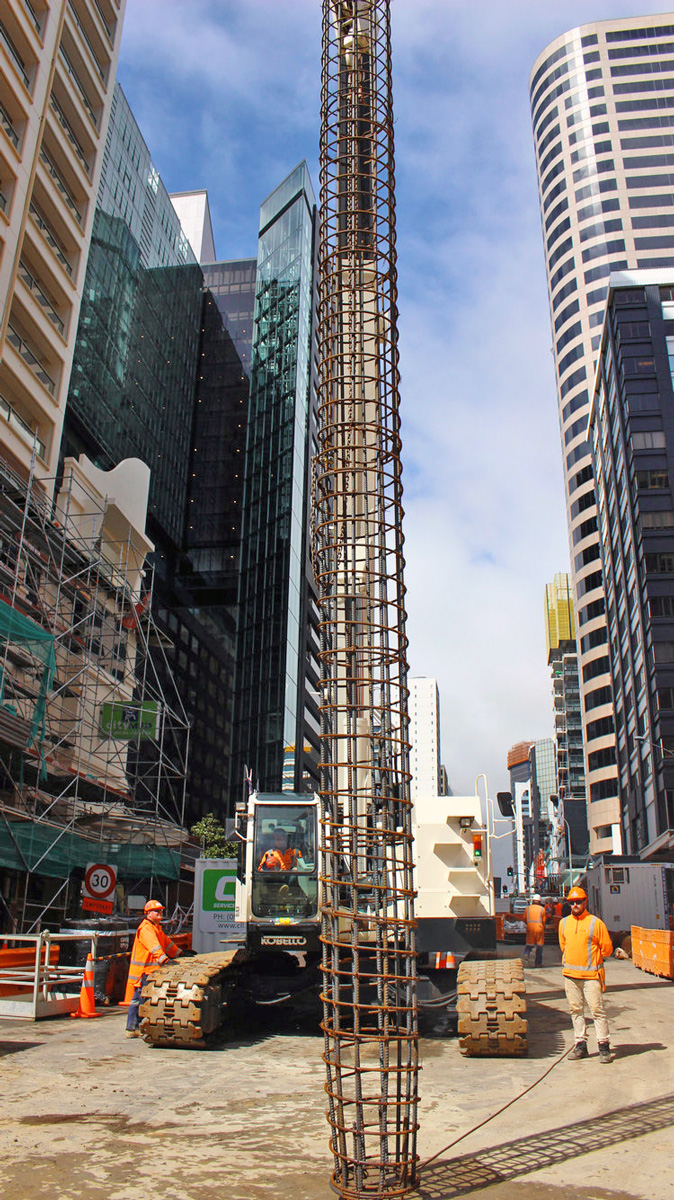
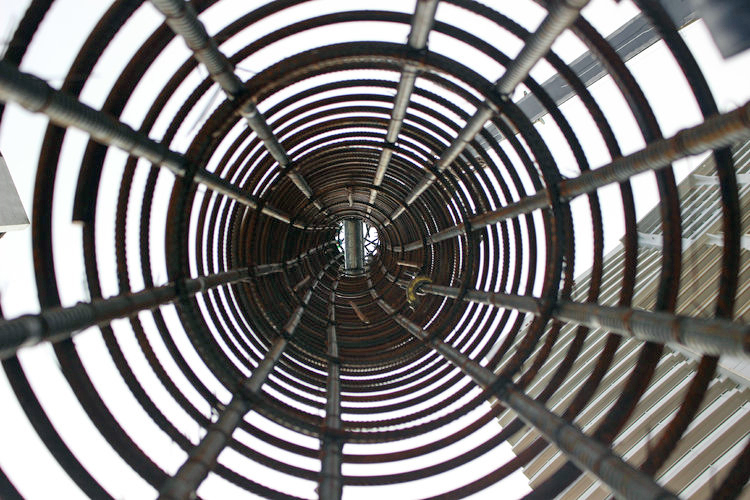
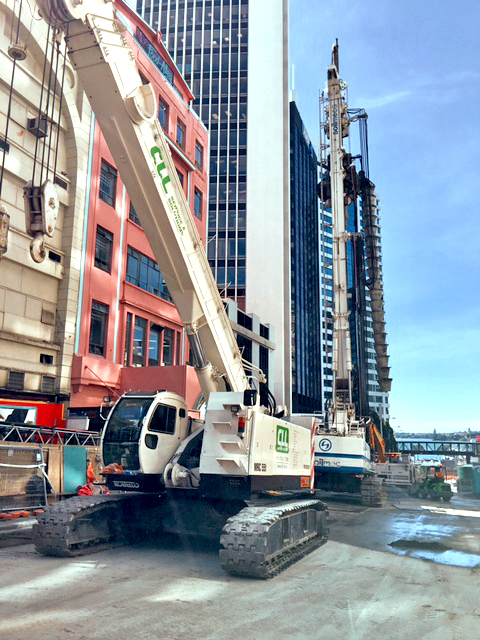
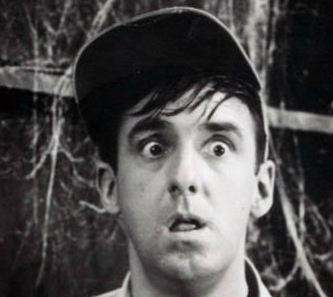
Sandrine
This bright red 90 tonne piling rig named Sandrine initially worked inside and outside the historic Chief Post Office building,
It was returned to France in early 2018 before being returned to work for Link Alliance’s construction.
The rig played a major part in preparing for the tunnel construction under the Chief Post Office building. The rig first began work around the outside of the building in Lower Queen Street and then in September 2017 was brought into the actual building.
With Sandrine's help, 64 diaphragm walls (or D-walls) were built by the Downer NZ Soletanche JV CRL construction workers. The wall panels form the structural support for the tunnels built in the building and also prevent water ingress.
A D-wall is a continuous wall constructed in the ground, typically to form an underground barrier or structure. They are constructed by an engineered fluid, typically a sodium bentonite mud, which is later replaced by permanent concrete. Sodium bentonite is an absorbent clay that expands when wet. Bentonite slurry (a mix of bentonite powder and water) was pumped into the trenches being excavated for the diaphragm walls to ensure the sides don’t cave in and ground water levels remain constant.
The walls were part of the permanent structure being built by supporting the building and the CRL tunnel box.
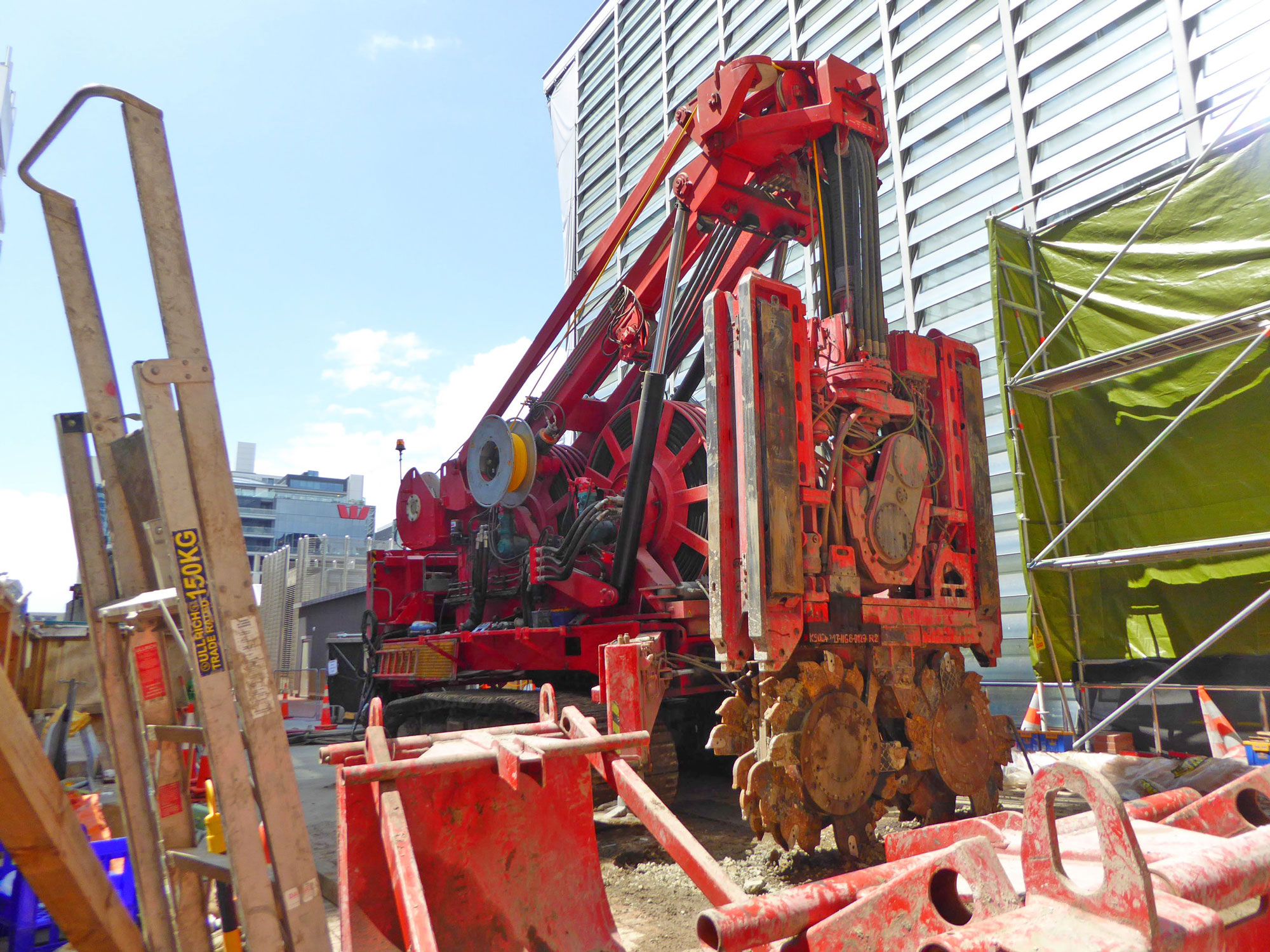
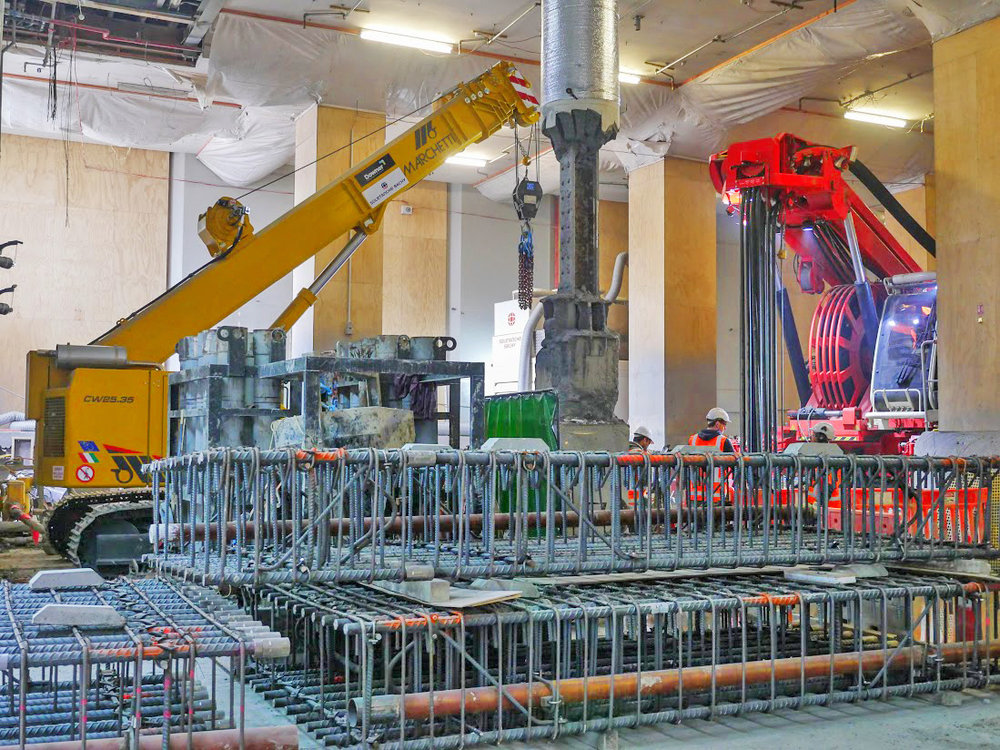
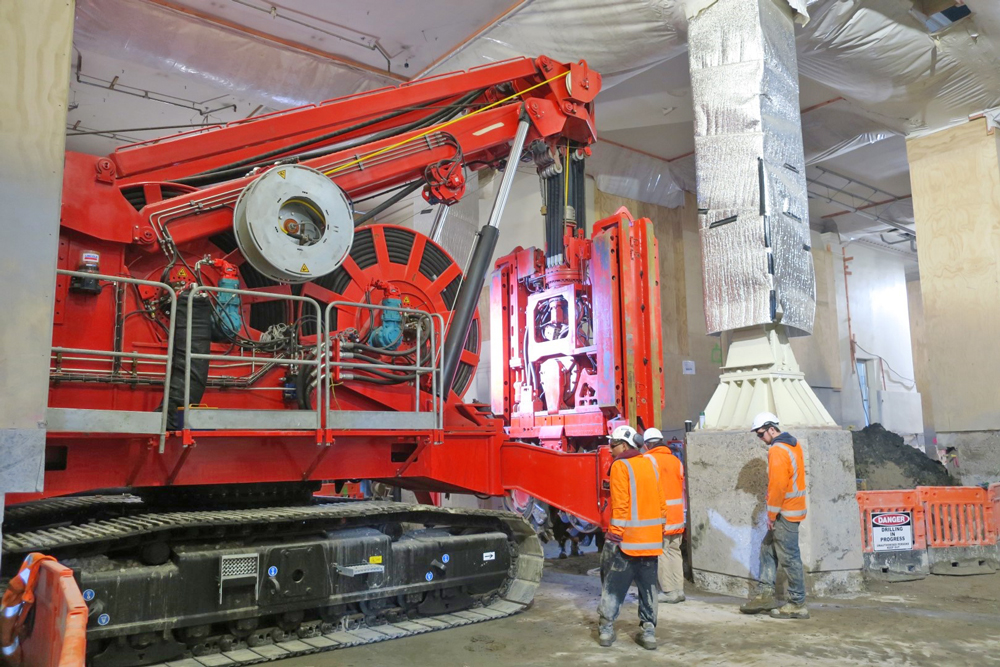
Sandrine is a compact hydrofraise piling rig - explained below.
And the name Sandrine?
Soletanche Bachy has a tradition of naming its machinery after women who work for the company.
The rig is named after Sandrine Mussier (pictured), who has worked for CRL contractor Soletanche-Bachy for the past 20 years, looking after its international project staff.
The return of Sandrine
Sandrine returned to the CRL project in June 2020 - to help with the Link Alliance construction of the Te Waihorotiu Station and Karangaa-Hape Station.
A ceremony was held on 23 June 2020 outside the station to mark the start of the construction with the machine about to make first cuts in the ground for the D-walls.
The Big Red Silos
During Sandrine's work at the CPO, passers-by got used to seeing the huge 10m high distinctive silos in Lower Queen Street. Those silos later re-appeared for the Link Alliance construction work on the Te Waihorotiu Station and Karanga-a-Hape Station.
The silos were part of a specialised bentonite plant, shipped over from France by CRL contractor Downer Soletanche-Bachy Joint Venture, to help with the construction of those diaphragm walls to support the CPO building foundations and the CRL tunnel box.
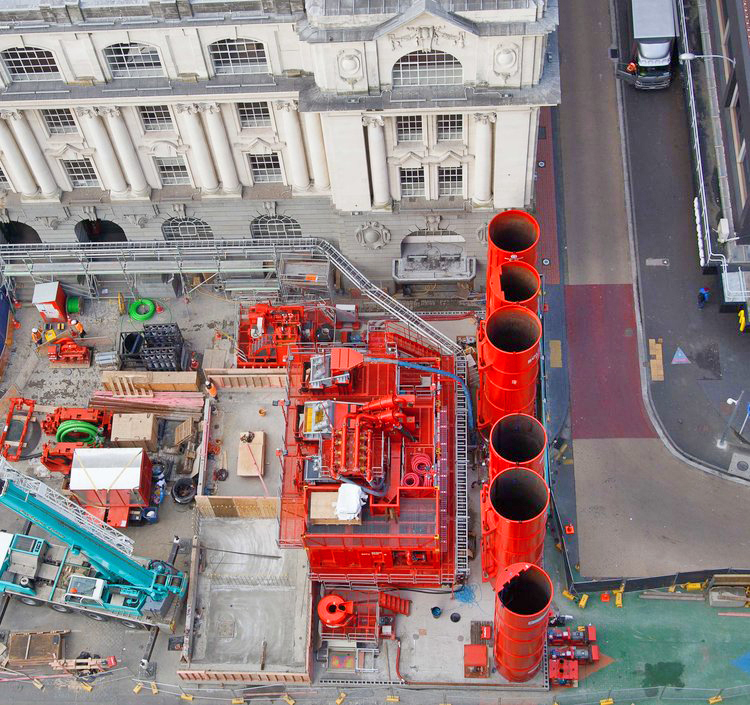
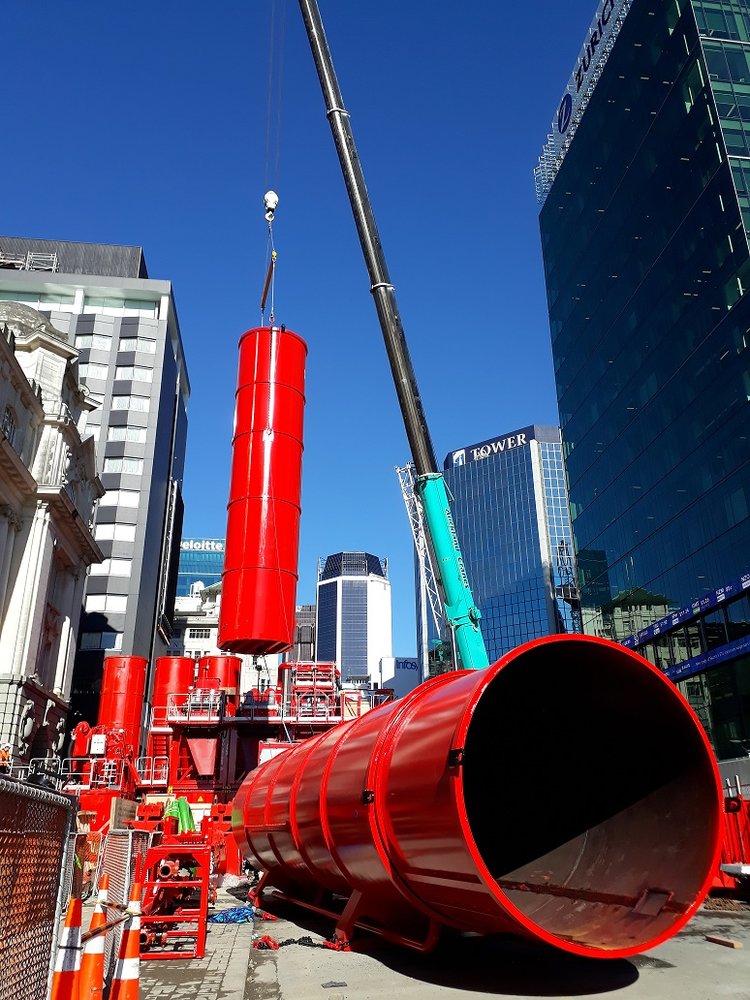
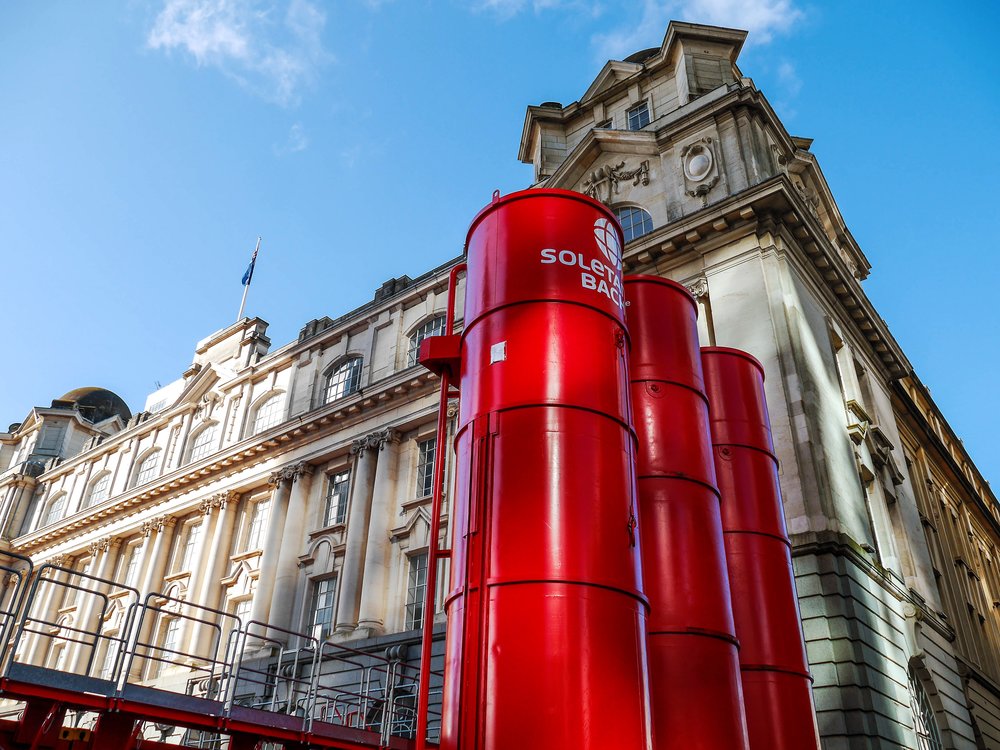
A similar Bentonite plant was set up for the Karanga-a-Hape Station.
Nine 12-metre red silos were brought in in May 2020 in the north-west corner (uphill on the East Street side) of the Mercury Lane construction site.
They were needed for the below ground construction of the station’s concrete walls.
Jean Batten (Road header)
Under Mercury Lane and the Link Alliance Karanga-a-Hape Station construction site, mined tunnel operations used a machine called a road header, named Jean Batten, in action under Mercury Lane.
Two road headers were used.
This excavating equipment consists of a boom-mounted cutting head, a loading device usually involving a conveyor, and a crawler travelling track to move the entire machine forward into the rock face. According to Wikipedia, the first use of a roadheader in a civil engineering project was the construction of the Melbourne underground rail loop in the 1970s, where the machines enabled around 80% of excavation to be performed mechanically.
The TBM was not used for the Karanga-a-Hape-Station. Instead the two road-headers were lowered down the temporary shaft to excavate the 220-metre platforms, tunnel cavern and adits between Mercury Lane and Beresford Square.
The TBM was pushed through this already mined tunnel as it makes its journey from a redeveloped Maungawhau Station to the new Te Waihorotiu Station and Karanga-a-Hape Station.
The name
Link Alliance’s Karanga-a-Hape Station team asked a local primary school, Kadimah. The teachers then ran a competition with a focus on engineering and the CRL project on Kadimah's front doorstep.
Year four student, Michael Krispin, was eventually selected as the winner for suggesting the name Jean Batten.
Michael's prize was a site tour with his father. They were led on a tour by the tunnel superintendent, Tomo Otene, and got to see inside the noise enclosure and have an up close look at the machine he named before it disappears underground for a year!
He said of Jean Batten: "She was a strong woman that was determined to make a mark in the world of aviation when it was dominated by men. She showed strength to fly the hours that she did."
George the crane
Even a big crane has to have a name.
The crane at the Link Alliance Te Waihorotiu Station construction was so impressive, the team thought it needed a name so they chose George.
The original Greek form of this name, Georgios, is based on the Greek word "georgos", which means "farmer". The word georgos itself is ultimately a combination of two Greek words, "ge", meaning earth or soil, and "ergon", which means "work".
Jeffie
A tunnel boring machine was needed to kick off CRL preparation work at the Maungawhau Station site.
In early 2018, contractors started diverting a section of the existing Mt Eden stormwater pipe and creating a new alignment between Water and Nikau Streets so that CRL could create a redeveloped train station.
The existing stormwater pipe was in the path of the new CRL tunnels that will be built there.
At Mt Eden, shafts at Water and Nikau Streets provided underground access for the micro tunnel-boring machine simultaneously excavating and installing the new stormwater pipe using a pipe jacking technique and a deep access chamber at Mt Eden Road.
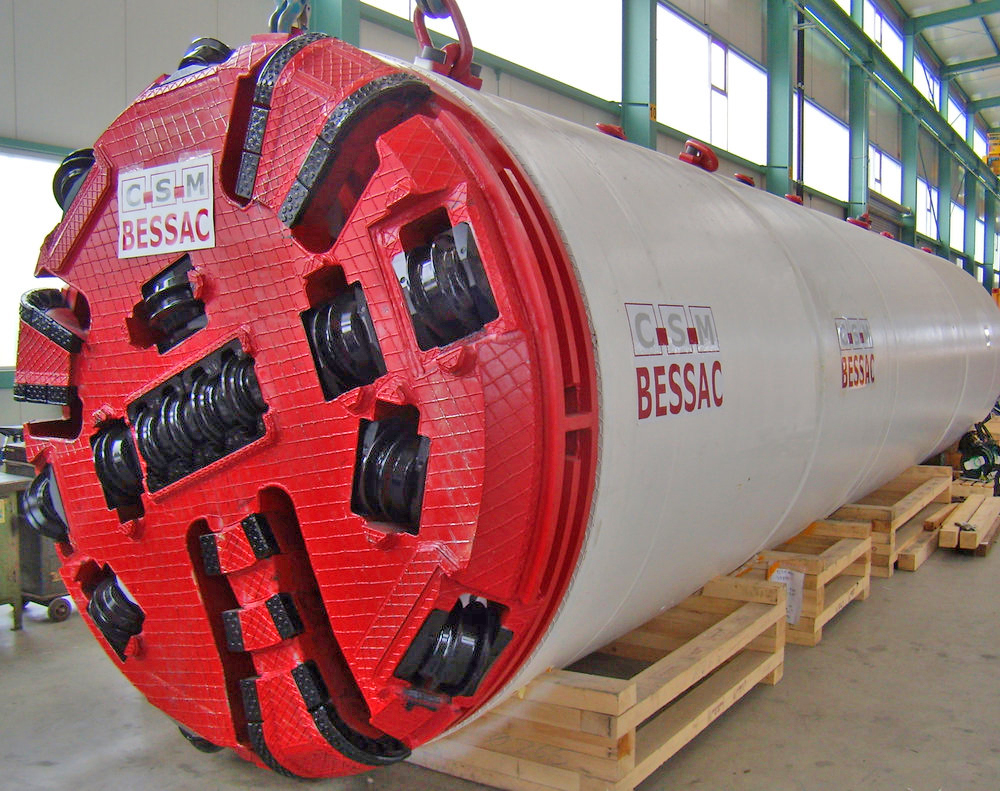
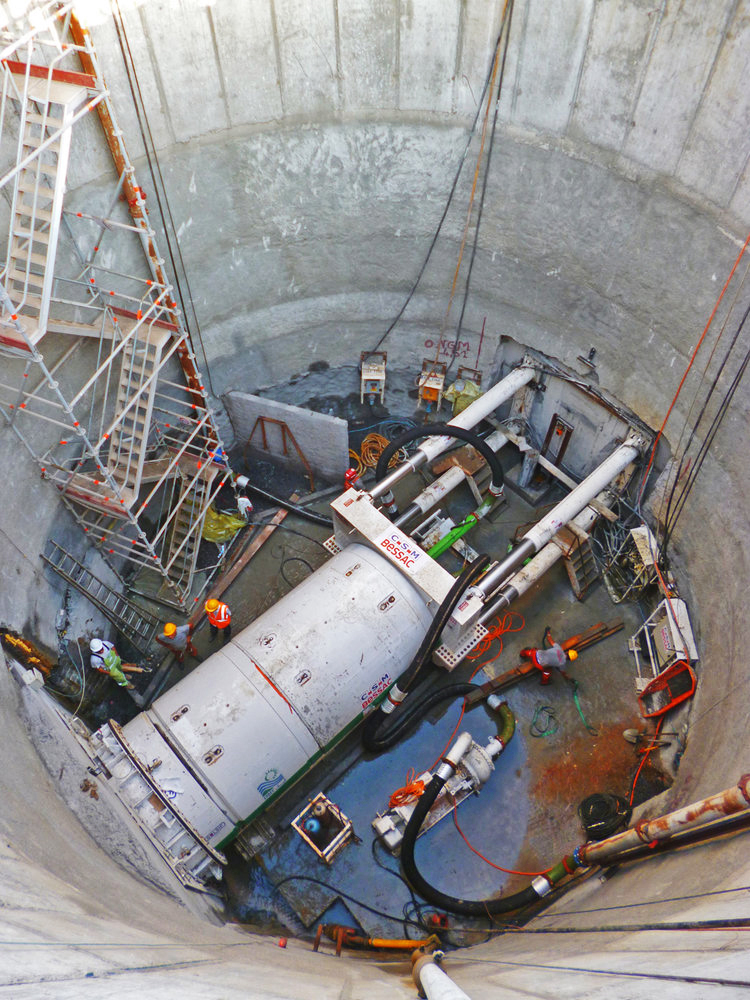
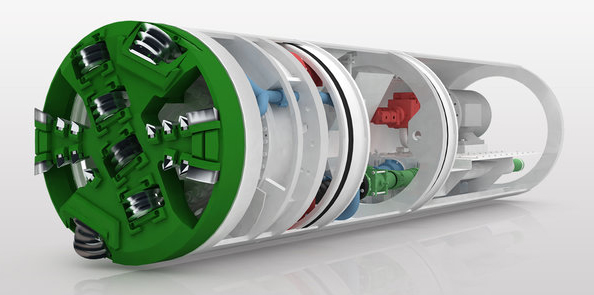
And the tunnel boring machine’s name?
Naming digging equipment after women is said to be a tradition that dates to the 1500s when miners prayed to St. Barbara to keep them safe underground. Saint Barbara is the patron saint of armourers, artillerymen, military engineers, miners and others who work with explosives because her legend associated her with lightning.
More than 30,000 people from as far away as the UK, USA, Europe, the Philippines and Afghanistan participated in the naming contest run in just under a week on CRL's Facebook page.
The most popular name by far was Jeff.
Thousands of people voted Jeff based on the popular meme “My Name is Jeff” which was a line used by the character Greg Jenko in the 2014 action comedy film 22 Jump Street.
So Jeffie, an aligned feminine name was used. Jeffie was a popular girls name in the early 1900s.
Explaining construction terms
Bentonite
Sodium Bentonite is an absorbent clay that expands when wet. In civil engineering applications bentonite is used as a mineral hydraulic barrier in diaphragm walls, foundations, tunnelling, horizontal directional drilling and pipe jacking.
Bentonite slurry walls (also known as diaphragm walls) are used in construction, where the slurry wall is a trench filled with a thick mixture of bentonite and water. A trench that would otherwise collapse due to the hydraulic pressure in the surrounding soil is prevented from collapsing as the bentonite slurry balances the hydraulic pressure. Forms for concrete, and rebar, can be assembled in a slurry-filled trench, and then have concrete poured into the form. The dense liquid concrete displaces the less-dense bentonite slurry and causes the latter to overflow from the trench. The displaced bentonite slurry is then channeled to a recycling unit from which it can subsequently be reused in a new trench elsewhere on the construction site.
BENTONITE: Bentonite was utilised while digging the structural support for the tunnel walls to ensure the excavation doesn’t cave in on itself.
HYDROFRAISE: This hydrofraise machine outside the Chief Post Office was used to dig the wall panels which form the structural support for the tunnels. This machine used the bentonite plant to dig down about 15 metres
JUNE 2017- Bentonite plant foundation slab prior to a 240m3 concrete pour.
SILOS: Outside Waitematā Station June 2017
Diaphragm Wall
A diaphragm wall (or D-Wall) is a continuous wall constructed in the ground and typically to form an underground barrier or structure. Diaphragm walls are constructed through a narrow trench, excavated in ground and supported by an engineered fluid (typically a sodium bentonite mud) which is later replaced by a permanent material (concrete).
A diaphragm wall would typically be constructed as a ‘perimeter’ to prevent water ingress, for example.
DIAPHRAGM: Constructing a diaphragm wall with steel reinforced cage - Commercial Bay
WALLS: Diaphragm walls in cut and cover tunnel construction
For the Beresford St entrance of the Karanga-a-Hape Station, construction of Diaphragm walls to form the station box was a process taking five months. These walls were the first permanent elements of the station to be built at Beresford Square. In total the station box is comprised of 30 panels ranging in depth from 18 – 39 metres.
There are four distinct phases for each D-wall panel installation, a process that takes two – three days to complete. The photos show the stages:
A grab rig excavating through clay to the rock layer approximately 10-metres beneath the surface.
A hydrofraise machine then uses twin cutting heads to excavate further through the rock, to a depth of up to 39-metres. Throughout the process bentonite slurry is pumped through the excavation to remove the cuttings from the excavation.
A steel reinforcing cage is lowered into the trench.
Concrete is then poured through a pipe into the bottom of the trench, displacing the bentonite which is pumped back into the bentonite plant.
D-wall panels are not installed sequentially next to each other as you might expect. The grabber and hydrofraise machines are too large to work side-by side, so panel installation will often move from one end of the square to the other, as shown below.
The first D-wall panel was installed adjacent to Pitt Street, with the second panel installed at the other end of the square near Samoa House Lane. This complex staging arrangement continued until all the panels have been installed.
The diagram shows the order in which the D-wall panels will be sequenced.
In October 2020, Link Alliance workers completed the D-walls at Mercury Lane. In total, 26 D-wall panels were installed below ground to form the station box.
Caisson
A caisson is a watertight retaining structure.
It can be used for, say, the purpose of gaining access to an existing underground service but in the case of the CRL, it was for forming reception shafts for the pipe jack works along Albert Street and at the points of connection between the new line and existing lines.
Segmented caissons are formed to create permanent portal entries to enable the Microtunnel Boring Machine (MTBM) to bore new stormwater pipes.
There were caisson shafts at Wellesley Street and a second shaft at Swanson Street.
Secant Pile Walls
Secant pile walls are drilled piles constructed in such a way that the piles overlap each other to form a wall. This is done to find drilling soft piles in hit and miss sequence and then drilling hard piles to interlock with the soft piles.
Secant piles are used to build cut-off walls for the control of groundwater inflow and to minimise ground movement.
Soldier piling
Soldier piled walls are effective as a temporary means of retaining the sides of bulk excavations and to form the retaining structure along Albert Street to enable construction of cut and cover tunnels.
Soldier piling was also used to construct two deep access shafts at the Victoria and Albert Street intersections to create a cavern to enable the Orakei Main Sewer to be bridged and strengthened.
Soldier piles are constructed of wide flange steel H sections spaced at intervals of 2 to 3m apart, driven in prior to excavation.
As excavation proceeds, horizontal timber sheeting (lagging) is inserted behind the H pile flanges.
H BEAMS: Wide flange steel H Beams
SOLDERING ON: Soldier piling for the OMS shaft at 'Victoria 2' - Victoria Street
Utility Diversions
In order to clear the way for CRL construction the diversions of many essential utilities is required. This includes stormwater, water, and wastewater pipes, electricity cables, telecommunications cables, gas pipes, and any other service conduit that needs to be safely relocated for the benefit of the service providers and their customers.
MYSTERY HUNT: Potholes are dug in streets such as here in Albert Street to find out what utilities are beneath the surface. Existing As-built records can be notoriously inaccurate and/or vague especially if those records are decades old, so identifying the owners of the utilities can be quite a task if the utilities are found to be not where the records say they should be!
Here is an example of the challenge. This is a patch of Customs Street:
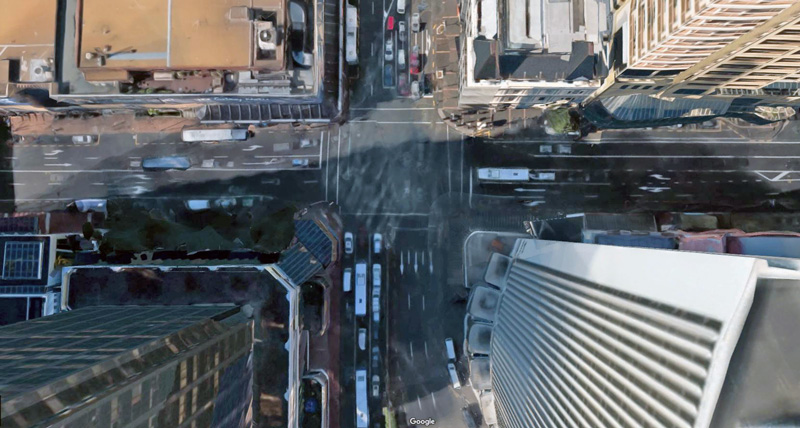
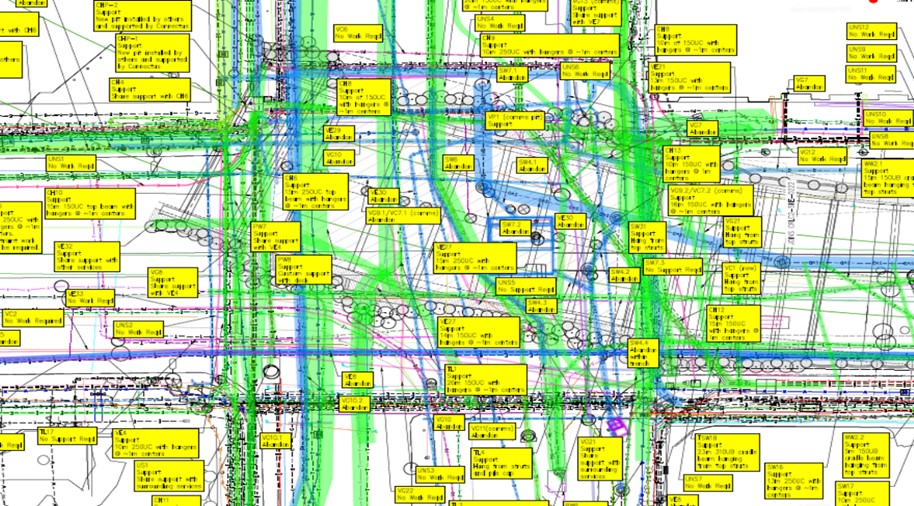
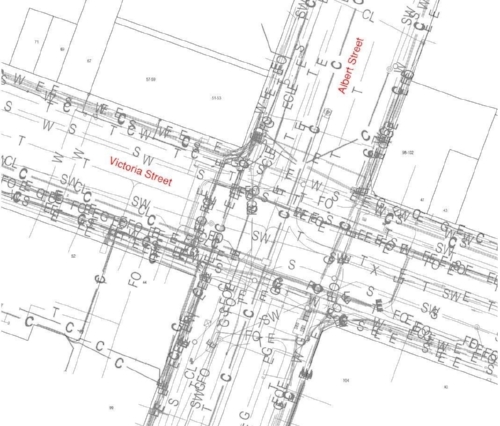